RESOURCES
BLOG
Join in the community forum! The thINK blog is a place for community members to share their opinions, best practices, successes, and challenges. Add your comments to the blogs published here or write a blog and we’ll post it for you.
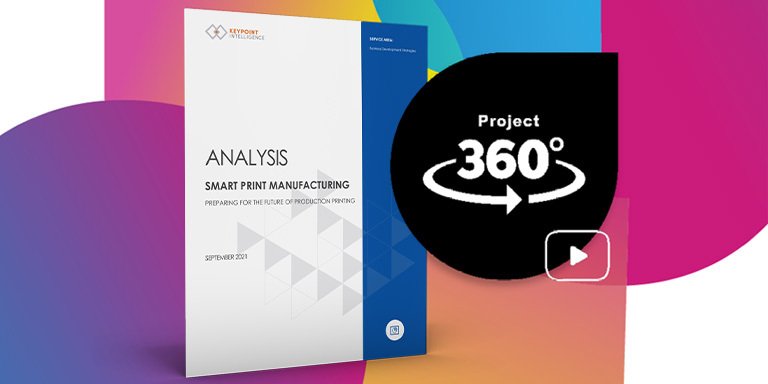
Smart Print Manufacturing
The Obstacles (Opportunities)
Industry analysts rightly point out that 2022 has many obstacles ahead. And as good businesspeople we know that an obstacle at its core is an opportunity. The short list of what we all face is Supply Chain issues, slowing growth, inflation, and workforce issues.
Canon and NAPCO Research held a webinar to present and discuss Top Trends for 2022. The short list above was covered and discussed in the nine trends identified by Canon’s sponsored NAPCO research.
As an Advisor within the Project 360 team at Canon, my role is to help our existing customers and our potential customers with identifying and improving productivity concerns. And with the opportunities ahead, productivity will be key.
The short list above directly targets margin. Productivity will be a key tool in protecting and perhaps growing margin in 2022. In the past we could adjust for margin pressure via workforce reduction. Not in 2022. We could overcome supply chain and raw material issues with finished good cost increases. Not in 2022. This is the year we embrace print as a manufacturing process and enable productivity through Smart Print Manufacturing!
Smart Print Manufacturing
It’s a fancy name. It has an acronym (SPM). Still at the core of Smart Print Technology is basic fundamental business processes. Keypoint Intelligence, in their white paper from September 2021, identifies “The Five C’s” of Smart Print Manufacturing: Consolidate, Connect, Collect, Compute, and Create. Let’s look at each.
Consolidate: Keypoint Intelligence says, “Start at the beginning by consolidating your production workflow processes with an automated workflow.” Easy, right? Well, it may be! We know our businesses well enough to know when a particular workflow process needs to improve, when it needs to go from a manual to an automated process. This is the year to execute!
Connect: Connect all hardware and software, as well as the business processes. This will, in many cases, need capital investment. In my humble opinion it is the correct investment for 2022.
Collect: This area is key. Data must be viewed as a raw material, and it must undergo rigorous quality control measures. Bad and/or faulty data will bring down a manufacturing process just as fast as a broken part. Two key sub-areas to improve: how we collect from our customers and how we collect internally.
When collecting from our customers we need a solid, well-documented, and enforced ETL (Extract, Translate, Load) platform and policy. At this point we can institute the rigorous data quality measures. Ensure your ETL process can export out to a large variety of data transport formats used by downstream processes.
When collecting internally we need to open ourselves to collecting and storing any and all data captured within our Hardware, Software, and Business processes. Be the source of your own Big Data. Have all of that information available to you to analyze, share, and use as a tool to set yourself apart from others.
Compute: Following a Best Practices approach in the collect phase lays the foundation for excellence in the Compute phase. When our data has been collected and stored via a well-documented and enforced ETL process the compute capabilities and processes expand. Keypoint Intelligence saw the use of cloud-enabled software increased by as much as 94% year-over-year when COVID-19 hit. Cloud computing is a tremendous tool; exploit it via the Smart Print Manufacturing 5-C’s.
Create: This is the End Game! It is what we do. We create for our customers. The foundations laid out here allow you to create with variety, creativity, and confidence. Multiple tools are available because you have designed and automated your workflow for flexibility. You can say yes to your customer!
Canon Project 360 team is here to help
At Canon, we work with our customers to continue to gauge progress and identify workflow needs as they emerge or change, and present new ways of completing work in a more timely and cost-efficient way. Our Project 360 initiative helps customers attract new business, grow print volumes, and turn around their operations for improved bottom-line results.
Free of charge to Canon inkjet customers, Project 360 is designed to broaden the scope of services that customers receive when they purchase an inkjet press. Most customers already leverage Canon’s Professional Services Analysts and Advisors in the months immediately following installation, but Project 360 is intended to provide support further out — even several years later. If you need help transitioning more of your work to your installed inkjet press, or if you seek new ways of completing work in a more timely and cost-efficient way, call in the experts. You can reach us at Project360@csa.canon.com